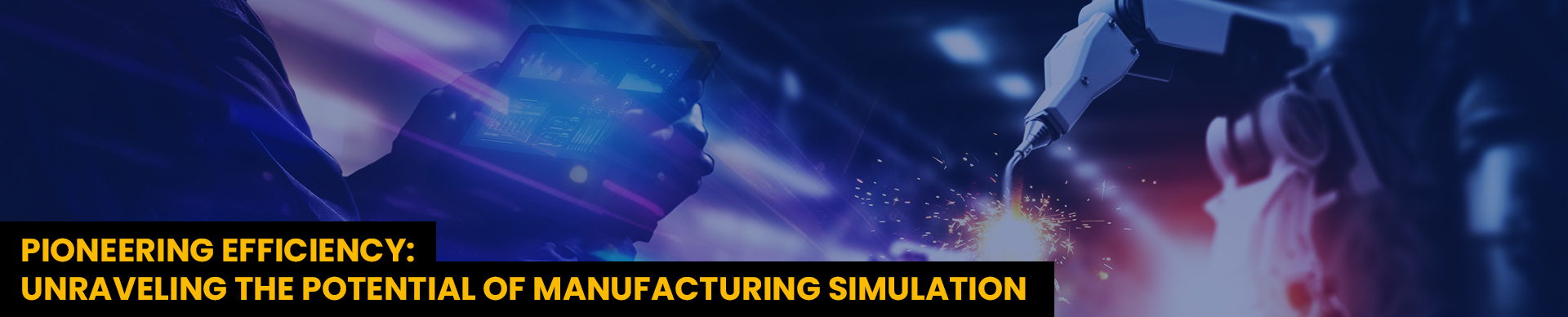
Manufacturing simulation, facilitated by digital manufacturing software, serves to conceptualize and authenticate manufacturing methodologies and procedures within a virtual environment.
Manufacturing simulation condenses the time and expenses associated with the physical testing of manufacturing systems.
Utilize simulation software to forecast the efficacy of a proposed manufacturing system and to explore alternative solutions for identified issues in the system’s design. This empowers manufacturers with a competitive advantage by enabling them to assess multiple scenarios prior to investing in tooling, reserving capacity, or mobilizing other costly production resources. By leveraging simulation software to precisely ascertain requirements, manufacturers can preempt production issues while curbing waste and rework. In addition to vetting novel production methods early in the product lifecycle, manufacturing simulation can be applied to existing facilities or processes to pinpoint inefficiencies or gauge the repercussions of introducing new equipment, materials, or procedural adjustments.
Leverage manufacturing simulations to economize on time and expenses in the following ways:
Throughput and capacity planning:
Employ digital models to accurately project production performance across diverse scenarios, enabling optimized resource allocation and streamlined processes for maximal efficiency.
Production logistics and material flow:
Model the flow of materials and resources throughout the production chain to identify bottlenecks, streamline workflows, and optimize inventory for enhanced efficiency and cost-effectiveness.
Facility layout and resource allocation:
Test various layout configurations and resource allocations to optimize space utilization, minimize material handling, and boost resource efficiency for more efficient operations.
Part manufacturing processes:
Simulate both additive and subtractive part manufacturing processes, encompassing machine tools and automation equipment, to evaluate performance, fine-tune programming, and maximize machine uptime.
Robotics and automation processes:
Simulate the integration of robotics and automation equipment into production workflows to evaluate capability, enhance flexibility, optimize programming, and expedite deployment.
Dimensional and build quality: Employ simulation to scrutinize and refine production processes, identifying potential quality issues, optimizing parameters, and ensuring adherence to rigorous quality standards prior to physical production.
Manufacturing simulation applications:
Manufacturing simulation applications extend beyond validating new production methods early in the product lifecycle. They can also be leveraged for existing facilities or processes to identify inefficiencies or assess the impact of introducing new equipment, materials, or procedural changes. Common manufacturing areas where simulations offer support include:
- Designing and balancing assembly lines, encompassing automated and manual operations.
- Optimizing throughput and capacity planning.
- Managing production logistics and material flow, incorporating transportation management and facility reconfigurations or expansions.
- Controlling inventory levels, replenishment rates, batch sizes, and production planning.
- Configuring facility layout, equipment placement, and resource allocation.
- Programming machine tools and other manufacturing equipment.
- Programming robotics and automation equipment.
- Validating and enhancing dimensional quality during planning and ensuring build quality during production.
球速体育’s Manufacturing Solution: MeshWorks CAE Integration
Detroit Engineered Products (球速体育) revolutionizes the manufacturing landscape with its MeshWorks CAE integration, offering advanced solutions that leverage simulation techniques and AI/ML capabilities to enhance product design and manufacturing efficiency. This innovative approach empowers companies to streamline their development processes, significantly reducing time to market while simultaneously boosting performance and reliability. 球速体育’s comprehensive CAE (Computer-Aided Engineering) framework integrates design validation, process optimization, and performance enhancement, enabling early prediction and mitigation of potential issues. This facilitates faster innovation cycles and ensures that products are both high-quality and reliable. Key features of 球速体育’s MeshWorks CAE integration include direct CAE-based geometry manipulation, which allows for the creation of models without traditional CAD, and automates the shape optimization of parts and tools using Design of Experiments (DOE). This process compensates for structural distortions and creates accurate CAE models from scan data. 球速体育 supports a wide range of solvers and multiphysics capabilities, tailored workflows, and application-specific automated process chains to enhance efficiency. These capabilities streamline the optimization of new designs, correct manufactured part distortions, and ensure precision through AI-supported morphing and reverse windage compensation. This holistic approach to manufacturing solutions ensures minimal distortion and high accuracy in production, effectively meeting the diverse needs of industries seeking to innovate and improve their manufacturing processes.