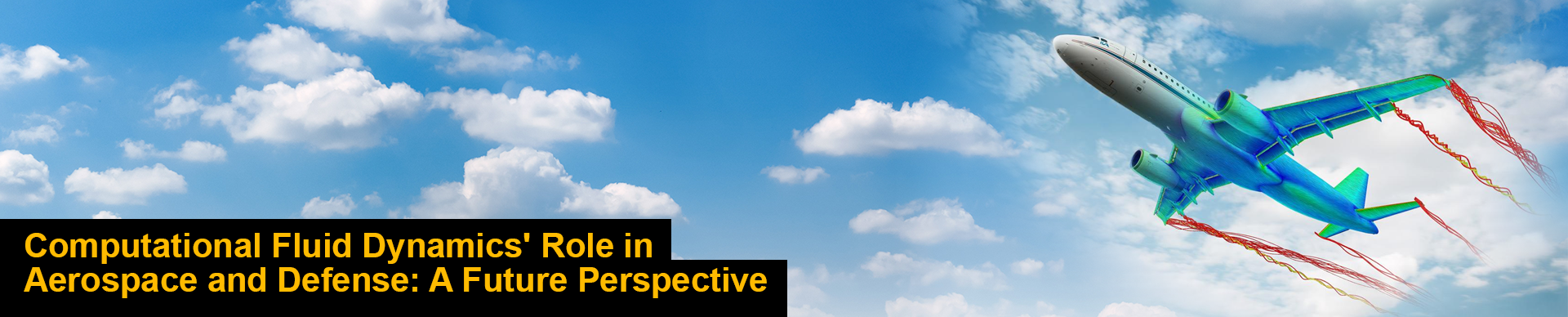
Computational Fluid Dynamics’ Role in Aerospace and Defense: A Future Perspective:
Aerodynamic design has become increasingly important as there is an increase in need for more optimized solutions. CFD can provide a detailed analysis of a flow field around or through an aircraft or its components, and is increasingly being used in multi-disciplinary design and analysis of aerospace products. Before costly prototypes and physical tests, it is used to analyze, validate, and optimize the performance of any product. The CFD tools can depict the products’ unseen characteristics while also investigating the flow& friction at various points. As a result, the design can be promptly iterated and optimized based on the outcome in order to meet performance and safety standards.
CFD performed sooner in the product development cycle increases the ability to optimize any product in terms of lowering emission and operational cost by providing detailed information about design parameters, giving engineers the ability to isolate physical process for detailed study. All of these features makes CFD one of the most reliable and crucial aspect of the entire product development cycle. Pressure drop, fluid temperatures, fluid mixing, aerodynamic lifts, and chemical reactions within the surfaces are some of the key aspects that come into play during a CFD analysis. Understanding each component will aid us in better positioning the product parts & design them for optimized performance. With the advancement of AL/ML/IoT, more precise solutions are now available, as real-time data can be turned into test cases.
CFD & Aerospace Industry – Aerodynamics Design through Virtual Validation:
Virtual validation is increasingly being used for design exploration and trade-off analyses in a variety of industries, including aerospace, automotive, and heavy industries. Engineers can now simulate and optimize designs faster than ever before thanks to faster high-performance computing (HPC). The situation is similar in aerodynamics research. Grid generation for modeling complex flow physics requires robustness, flexibility, and automation. Engineers can now study the flow over the fuselage and wings, as well as around the nacelles and air intakes. Aerodynamic virtual validation is now being applied to cargo planes and surveillance drones in addition to commercial airlines.
The following are some of the ways that CFD plays a significant role in the aerospace industry:
-
External flows:
- Lift and drag forces
- Aerodynamic Shape Optimization
- Dynamic Pressure on Materials
- Structural Analysis
-
Internal flows:
- Pressurized Cabins Simulate pipe flows, turbulence in pipes, pipe shocks, cavitation damage, and so forth.
- Nozzles, Diffusers, and other components design
-
Multi-phase flows:
- Droplet dynamics
- Air-fuel mixtures
-
Reacting flows:
- Combustion Aerodynamics
- Fuel Burning Rate
- Turbulent combustion
- Thrust obtained
Limitations of CFD implementation in Aerospace and Defense application:
CFD capabilities have changed and evolved with computational technologies. Many fluid engineering problems are now simulated, but most of them are at the single-component level. More inclusive modeling, such as pump systems; in general, coupled with subsystems that are dependent on each other, will be required to reap the full benefits of CFD. Attempts to solve these types of problems have yielded some notable successes. However, the predictive capability is still very limited, and accurate physics prediction is still a long way off. Above mentioned data necessitates the inclusion of modeling of not only fluid dynamics but also other quantities such as thermal loading, turbulence and transition prediction, droplet formation, separation, and cavitations physics.
Other factors limiting the use of CFD in the design and creation of databases, as well as in multi-disciplinary applications, is the turnaround time associated with CFD and the level of expertise required of the CFD user. A long lead time may be required for a CFD user to become proficient in all phases of CFD (geometry preparation, gridding, solution set-up, post-processing).
Additional constraints in CFD includes numerical uncertainties, physical modeling (particularly transition and turbulence), and the time required to prepare geometries for grid generation and aerodynamic analyses.
球速体育 Services:
球速体育’s extensive range of services starting from Aerodynamic simulation helps in optimizing the aerodynamic drag, providing cooling simulations, Turbocharger Flow analysis. We offer comprehensive CFD studies that results in optimization based on aero drag, load calculations, and other applications. Some of our major projects include CFD calculations to compute the structural loads caused by air pressure, applied to aircraft components and assemblies to ensure better performance in high velocity circumstances. These are critical features that require extreme precision since they come under safety protocols. 球速体育 can provide the best aerodynamics support for aero products design & development that substantially increases the efficiency, resulting in optimized performance.
To know more about 球速体育 Aerospace and Defense
To know more about Aerodynamics services
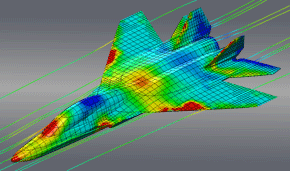
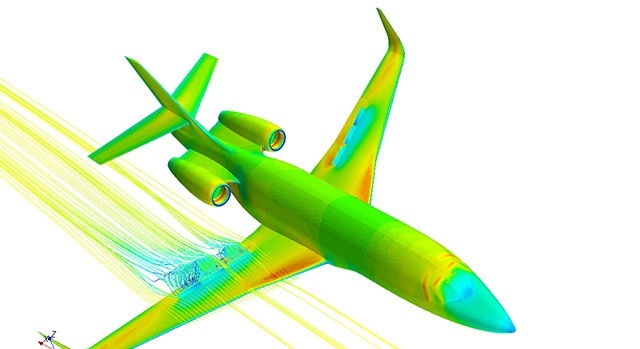
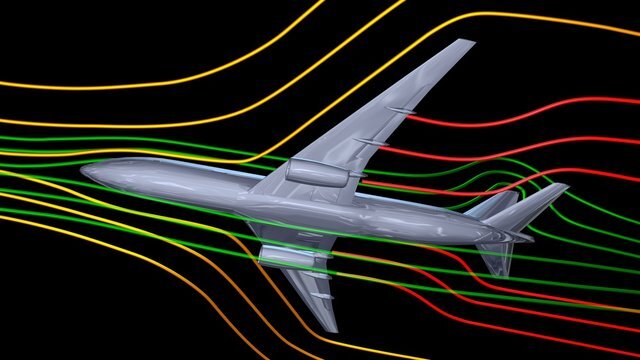
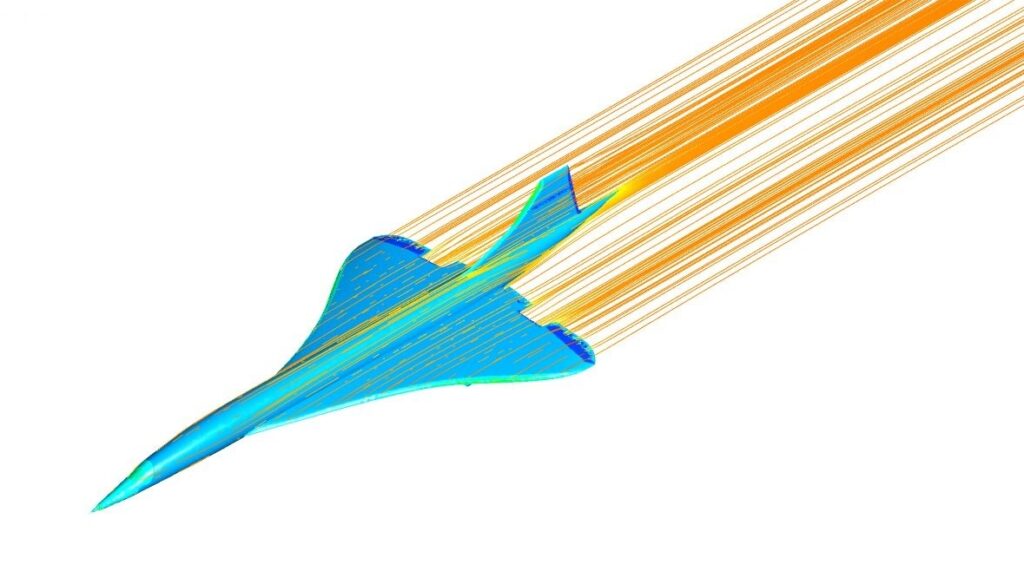
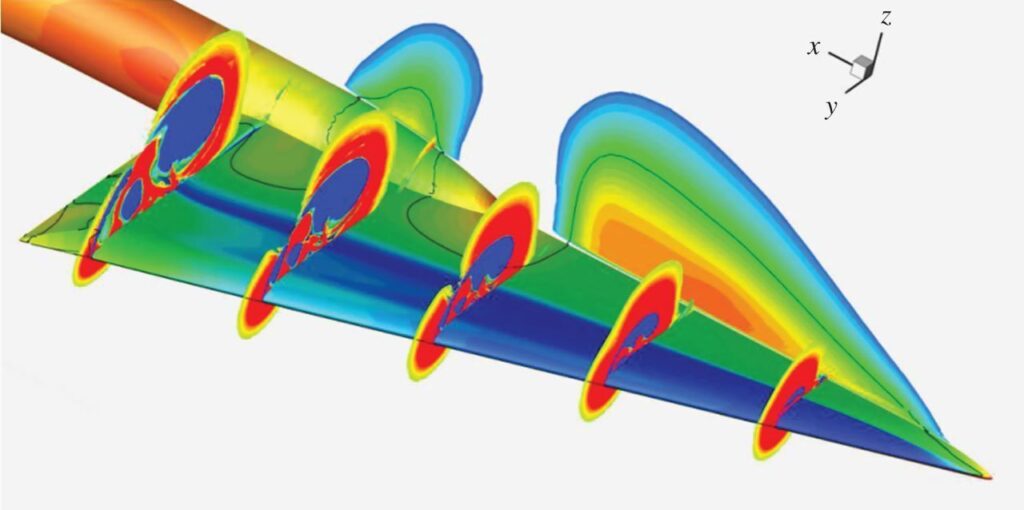
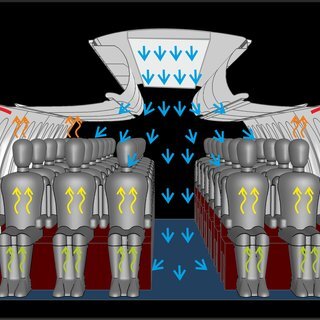
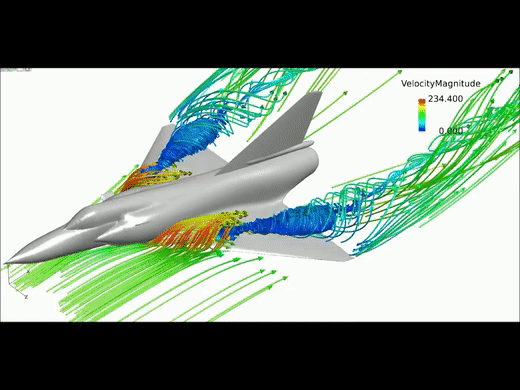